Exterior vehículo
Aplicaciones > ► Automotiriz > ► Exterior vehículo
Exterior del vehículo
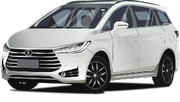
Aplicaciones exteriores
Los fabricantes de automóviles han reconocido los beneficios inherentes de los PAB para aplicaciones automotrices exteriores. Estos incluyen:
- reducción de peso
- consolidación / integración / reducción de piezas
- costos de herramientas reducidos
- mayor flexibilidad de diseño
- mayor robustez para impactos menores
Para cumplir con las ventajas indicadas anteriormente, hay varios factores importantes que deben tenerse en cuenta para la selección adecuada del material. Estos se pueden resumir como:
- acabado
- costo
- resistencia
- rigidez
- resistencia al impacto
- peso
- coeficiente de expansión térmica lineal (CLTE)
- resistencia química
- resistencia al impacto
- resistencia al calor
- resistencia a la corrosión
- pintabilidad en línea (requerido> 200°C de resistencia al calor, que solo PA / PPE podría cumplir, pero las temperaturas del horno ahora se reducen a, digamos, 120°C)
Las aplicaciones potenciales más grandes se encuentran en las áreas de paneles de carrocería verticales, que requieren una estética de superficie "Clase A". Debido a los requisitos extremos de resistencia a la fluencia de los paneles de carrocería horizontales, actualmente no se utilizan mezclas de polímeros para estas aplicaciones. Sin embargo, para paneles verticales, molduras, cubiertas de ruedas, etc., el comportamiento de fluencia no es tan crítico debido al menor peso no soportado de las piezas. El PC/ABS es uno de los PAB más utilizados para componentes de carrocería de plástico porque combina baja densidad (40% menos de peso que el metal en la misma aplicación) con alta tenacidad (menos del 20% de daño en impactos de 5 km/h). La tenacidad relativa en las pruebas de caída de la bola y el alargamiento por tracción son relativamente altas en comparación con el compuesto termoendurecible para moldeo en láminas y el uretano RIM. Uno de los mercados más grandes de paneles de carrocería de plástico es el automóvil Saturn de General Motors. Las aplicaciones exteriores en el Saturn incluyen:
- PC/ABS para puertas
- TPO para fascia
- PA/PPE para guardabarros delantero y paneles traseros
La mezcla de PC/ABS contiene aproximadamente un 8% de un relleno mineral para ayudar a la estabilidad dimensional. Es un excelente material para puertas debido a su impresionante resistencia a las abolladuras. Por ejemplo, se requiere una energía de impacto de 7,2 J para producir una abolladura de 1 mm en comparación con solo 0,9 J para el acero. El PPE/PA es el material de elección para guardabarros y paneles laterales debido a su excelente resistencia química a los derrames de gasolina y otros fluidos automotrices que se encuentran debajo del capó, muy cerca de los guardabarros delanteros. Cabe señalar que un uso tan extenso de PAB para paneles exteriores, en particular los paneles laterales, no sería posible en diseños de automóviles convencionales donde el panel trasero sirve como un miembro estructural integral. El PC/ABS de segunda generación tiene un sistema de relleno patentado que se dice que proporciona una estabilidad dimensional sobresaliente para aplicaciones en paneles de carrocería. El producto fue diseñado específicamente para sistemas de pintura que se curan a temperaturas inusualmente bajas (por debajo de 150°C), sin E-Coat. Para las aplicaciones que requieren resistencia a los solventes, donde se usa comúnmente PPE/PA, se espera que las aleaciones PC/PEST muestren una mejor estabilidad dimensional debido a una menor absorción de agua. El factor limitante para estas aplicaciones es su menor resistencia al calor. Uno de los factores más importantes que determinan la aplicabilidad de un PAB para el uso de paneles de carrocería es la capacidad del material para soportar altas temperaturas. Los paneles de carrocería de plástico generalmente ven uno de los tres posibles entornos de horno de pintura:
- Hasta aproximadamente 200°C en "pintura en línea", donde el panel de plástico se ensambla al vehículo antes de la alta temperatura del horno de recubrimiento resistente a la corrosión (E -Saco)
- Aproximadamente 140 a 180°C en “pintura en línea”, donde se elude el paso anterior porque la pieza se ensambla posteriormente al vehículo, pero la pieza de plástico debe pasar por hornos posteriores
- Aproximadamente 120 a 140°C en "pintura fuera de línea", donde los paneles de plástico se pintan independientemente del vehículo y se ensamblan como piezas pintadas
Para las dos primeras aplicaciones, las aleaciones PPE/PA han sido esencialmente los materiales de uso exclusivos. Para la tercera aplicación, se han utilizado PC/ABS y PPE/PA. Las mezclas de PPE y PA-66 son adecuadas para aplicaciones automotrices exteriores, donde producen superficies de clase “A” en los paneles de la carrocería, porque combinan la resistencia al procesamiento y a los solventes de las poliamidas con la resistencia a la humedad y la estabilidad dimensional del PPE. Por lo tanto, tienen buena resistencia al calor, resistencia al impacto, moldeabilidad, adherencia de la pintura y resistencia química. Comparando PPE/PA, PC/ABS y PEST/ABS, se pueden hacer las siguientes observaciones:
Ninguno es adecuado para paneles horizontales
CLTE todavía es demasiado alto - necesita tener un extremo libre para moverse
PA/ABS y PEST/ABS tienen DTUL demasiado bajo
PC/ABS tiene mejor impacto bajo T
PC/ABS tiene peor resistencia química
todos tienen suficiente resistencia al impacto
PEST/ABS tiene resistencia química moderada
PPE/PA tiene mejor DTUL y resistencia química
PA/ABS es demasiado sensible a la humedad
Los paneles de la carrocería con requisitos estéticos algo menos exigentes incluyen carenados de camiones. Las piezas extremadamente grandes como estas a menudo se fabrican mediante termoformado en lugar del moldeo por inyección. Por esta razón, es esencial una buena resistencia a la fusión. Actualmente se utilizan materiales PPE/PA en estas aplicaciones. Las fascias de los parachoques (TPO) están aumentando en superficie y se están integrando más en el diseño de la carrocería. La fascia del parachoques más delgada requerirá que el plástico sea más rígido, tenga mejores características de flujo de fusión y aún cumpla con los requisitos de resistencia al impacto de -30°C. Los parachoques de PC/PBT se reutilizan para las carcasas de las luces traseras de las camionetas, reemplazando al ABS de alta temperatura. Las ventajas son el ahorro de costes y la reducción de los requisitos de vertedero. Una viga del parachoques trasero moldeada por inyección de resina PC/PBT para el Saturn 1997 incorpora 13 partes previamente separadas. Se fija debajo de una fascia fl exible y contiene torres moldeadas que absorben la energía aplastando al impactar. La viga del parachoques pasa las pruebas del poste trasero del Instituto Federal de Seguros y Normas de Seguridad de Vehículos Motorizados para la Seguridad en las Carreteras. El sistema de parachoques ahorra 1,4 kg de peso incluso sobre el sistema de espuma de polipropileno / aluminio más ligero adoptado por Saturn en 1991. Además, el parachoques requiere menos mano de obra para sujetarlo al vehículo y se puede reciclar. Las mezclas de PU/PC utilizadas para parachoques blandos tienen una alta resistencia al impacto en el rango de -29 a 66°C, además de flexibilidad y pintabilidad. Se utiliza una mezcla de PC/ASA en partes exteriores como las rejillas de ventilación del capó, molduras, rejillas delanteras, biseles de faros delanteros, pilares, soportes de placa de matrícula y marcos de ventanas. La principal ventaja de esta aleación resistente a la intemperie es la eliminación de pintura, lo que reduce las emisiones de solventes del proceso. Los tanques de combustible con mejores propiedades de barrera que el HDPE solo se fabrican utilizando tecnología de moldeo por soplado de resina de barrera. El HDPE se mezcla con resina de barrera de PA/PE. Se puede usar una mezcla de uretano/ABS en lugar de ABS recto en la parte inferior de un carenado de chasis lateral de dos piezas para aumentar la resistencia a la fatiga del carenado. La parte superior del carenado está fabricada en poliéster reforzado con fibra. Las aleaciones termoplásticas basadas en estireno maleimida con PA tienen buena estabilidad térmica, resistencia química, resistencia a la abrasión, pintabilidad y resistencia a la intemperie. Los mezclados con ABS combinan resistencia térmica con muy buena procesabilidad. Las aleaciones se utilizan en varios componentes automotrices, como parrillas de descongelación, manijas de puertas y marcos de faros. Las aleaciones fabricadas combinando poliarilamida con PA y polipropileno (que podría estar ligeramente reforzado con vidrio) ofrecen una baja absorción de agua, incluso a altos niveles de PP, buena resistencia al impacto y menor densidad, lo que reduce el precio por volumen. Las aplicaciones específicas incluyen paneles de carrocería de automóviles y componentes eléctricos. Las mezclas de PMMA (polimetilmetacrilato) y ABS que son fuertes, resistentes al calor y a la intemperie y tienen buenas propiedades de flujo durante el procesamiento se utilizan en los marcos de los grupos de luces traseras de los automóviles. Las mezclas de PC/ABS se pueden usar en partes exteriores e interiores de automóviles, incluidas las vigas y fascias de los parachoques, cubiertas de ruedas, rejillas de ventilación del capó, molduras laterales de la carrocería, paneles verticales de la carrocería, spoilers, componentes del panel de instrumentos, salidas de aire, molduras decorativas, puertas de la guantera , cubiertas de postes de soporte y carcasas de espejos. Las mezclas de PC/ABS que tienen buenas propiedades de flujo, alta resistencia al calor y resistencia al impacto a baja temperatura se están utilizando para carcasas de indicadores delanteros de automóviles. Las cubiertas de las ruedas de los automóviles con tracción delantera deben soportar temperaturas de hasta 150°C. Por el contrario, las cubiertas de las ruedas de tracción trasera solo tienen un requisito de resistencia a la temperatura de 105°C y pueden utilizar cubiertas de ruedas de PC/ABS que son menos costosas. La aleación de PC/ABS de grado enchapado puede reemplazar las piezas de metal para automóviles debido a su mayor resistencia al impacto y al calor que el ABS enchapado tradicional y menor costo y peso que el acero inoxidable y el zinc fundido a presión. Otras aplicaciones exteriores incluyen carcasas de espejos, manijas de puertas, spoilers y cubiertas de ruedas. Cada una de estas aplicaciones se pinta fuera de línea, de modo que los requisitos de resistencia al calor permiten una selección de materiales relativamente amplia. En los últimos años ha habido una tendencia a avanzar hacia la deposición electrostática de pinturas para aplicaciones exteriores de automóviles. Las razones de esto incluyen una mayor eficiencia en la transferencia de pintura. Normalmente, las piezas de plástico deben pintarse con una imprimación conductora antes de la pintura electrostática de las capas base y transparentes. Uno de los desarrollos más recientes en el área de aplicaciones automotrices externas es el de las resinas intrínsecamente conductoras para pintura electrostática. Actualmente existen aplicaciones comerciales para paneles de carrocería que utilizan PPE/PA que contiene negro de humo como componente conductor. En los EE. UU., Una aplicación de carcasa de espejo utiliza PPE/PA donde la conductividad se logra mediante la incorporación de nanotubos de grafito. Los beneficios de los PAB conductores para la pintura electrostática se pueden resumir de la siguiente manera. Se observa una reducción significativa en el uso de capa base y capa transparente cuando se cambia de pintura tradicional a pintura electrostática de plásticos ordinarios. Sin embargo, primero se debe aplicar una capa de imprimación conductora. Cuando se emplea pintura electrostática de un plástico conductor, se mantiene una excelente eficiencia de transferencia de pintura, pero se elimina el paso adicional del proceso de imprimación conductora. Esto significa que las cabinas de pintura y la mano de obra asociada con la imprimación conductora se pueden entregar a las operaciones de base y capa transparente. Otro beneficio significativo de la pintura electrostática de plásticos conductores es que la reducción en el uso de recubrimientos reduce drásticamente las emisiones de compuestos orgánicos volátiles (COV). Si una operación de pintura está cerca de los límites legales de COV, es poco lo que se puede hacer para expandir la capacidad. Un cambio en la tecnología hacia plásticos conductores puede reducir los COV en la medida en que la capacidad se pueda incrementar de manera efectiva, sin gastos significativos para la planta y el equipo. Se han desarrollado mezclas de PPE/PA que proporcionan los beneficios descritos anteriormente al mismo tiempo que proporcionan la flexibilidad del moldeo por inyección y el rendimiento físico de una resina de ingeniería. Los paneles exteriores de la carrocería de los vehículos incluyen los paneles de las puertas, el techo, el piso, los guardabarros, el capó y los paneles traseros. Estas aplicaciones altamente exigentes requieren coeficientes de expansión térmica lineal (CLTE) muy estrictos y comparables a los de los metales, con resistencia al pandeo a alta temperatura para sobrevivir al alto calor de los hornos de horneado con electrorevestimiento en las líneas de ensamblaje de grandes plataformas de automóviles. (Las altas temperaturas en los hornos de horneado son necesarias principalmente para impartir resistencia a la corrosión al resto de la estructura de acero). Esto dificulta la entrada de plásticos porque los plásticos siempre se introducen con metales existentes y, por lo tanto, deben coincidir con las especificaciones de los paneles de la carrocería de metal. Por ejemplo, una cierta cantidad de conductividad superficial es esencial para permitir pintar lado a lado con metales en un solo proceso simplificado. Requisitos para diferentes áreas de aplicación en el revestimiento exterior :
Paneles de carrocería
Temperaturas en producción:
Horno de electrorrevestimiento hasta 200°C
Horno de cebadora hasta 185°C
Horno de esmalte hasta 160°C
Reparar horno hasta 140°C
Paneles horizontales hasta 90°C
Baja temperatura: hasta -40°C
En servicio a la luz del sol:
Paneles verticales hasta 75°C
Agentes químicos:
Gasolina, especialmente cerca de la entrada de combustible.
Alquitrán y sal, en los paneles inferiores, Abrillantadores de automóviles (generalmente abrasivos)
La estabilidad de la forma debe mantenerse a la temperatura superior; La resistencia al impacto debe mantenerse a la temperatura más baja. Se espera que las superficies sin pintar no se deterioren más rápido que las pintadas. Los parachoques (es decir, los extremos delantero y trasero) deben conservar la resistencia al impacto y la resistencia a la deformación de acuerdo con las normas especiales.
Muchos plásticos pueden soportar condiciones climáticas extremas, como los intensos rayos UV de la luz solar, los cambios rápidos de temperatura y las condiciones extremas de sequía y humedad, algunas de las cuales hacen que el metal sea una opción poco práctica. Los plásticos también pueden soportar el importante desgaste que presentan los terrenos difíciles. Nuestra amplia cartera de materiales tiene grados adecuados para una amplia gama de aplicaciones exteriores, tanto para piezas pintadas como sin pintar. PBT, ASA, PC/ABS, PP, PA satisfacen todas las necesidades de las piezas exteriores, con grados estabilizados a los rayos UV adecuados para piezas con formas complejas, incluidas las bases de los retrovisores exteriores, y piezas fabricadas mediante moldeo por inyección asistida por gas. Para las manijas de las puertas, nuestros grados especializados brindan una alta estabilidad a los rayos UV cuando no están pintados, y suavidad y excelente adherencia cuando están pintados. Para los espejos retrovisores exteriores, nuestros materiales combinan la estética con una alta rigidez y resistencia para lo que, en última instancia, es una aplicación de seguridad importante.
Revestimiento exterior
Los requisitos para el acabado exterior son básicamente los mismos que para los paneles de la carrocería. Algunos elementos se instalarán después de la línea de pintura, pero aún pueden estar sujetos a los hornos de reparación. Las lentes transparentes para faros delanteros y luces traseras deben cumplir determinadas especificaciones de envejecimiento con respecto a la retención del color, la resistencia al impacto, el rendimiento óptico y la resistencia a los arañazos. Los diseños de las molduras de las ruedas deben satisfacer los requisitos de resistencia al impacto, estabilidad de la forma (a las temperaturas de los frenos de disco) y pintabilidad.
Componentes exteriores del automóvil moldeados por inyección
El moldeo por inyección es la técnica ideal para fabricar una amplia gama de componentes exteriores de automóviles. Nuestro equipo de profesionales experimentados en moldeo por inyección trabaja en estrecha colaboración con los fabricantes de equipos originales (OEM) automotrices y los clientes de tier1 para evaluar y definir todos los requisitos técnicos y, por lo tanto, optimizar la producción de componentes exteriores impecables para vehículos. Somos fabricantes de moldes de inyección de plástico de partes exteriores de automóviles, por ejemplo: guardabarros (guardabarros), pasos de rueda, rejillas, soportes de sensores, rieles de piso, molduras de maletero, cubiertas delanteras y traseras, parachoques y molduras de puertas de automóviles, paneles de puertas . Nuestras piezas de plástico inyectado para automóviles se encuentran en una variedad de modelos de automóviles en todo el mundo. Los paneles exteriores de la carrocería de los vehículos incluyen los paneles de las puertas, el techo, el piso, los guardabarros, el capó y los paneles traseros. Estas aplicaciones altamente exigentes requieren coeficientes de expansión térmica lineal (CLTE) muy estrictos y comparables a los de los metales, con resistencia al pandeo a alta temperatura para sobrevivir al alto calor de los hornos de horneado con electrorevestimiento en las líneas de ensamblaje de grandes plataformas de automóviles. (Las altas temperaturas en los hornos de horneado se necesitan principalmente para impartir resistencia a la corrosión al resto de la estructura de acero). Esto dificulta la entrada de plásticos porque los plásticos siempre se introducen con metales existentes y, por lo tanto, deben coincidir con las especificaciones de los paneles de la carrocería de metal. Por ejemplo, una cierta cantidad de conductividad superficial es esencial para permitir pintar lado a lado con metales en un solo proceso simplificado. El primer uso industrial importante de termoplásticos (una mezcla rellena de policarbonato [PC] y acrilonitrilo-butadieno-estireno [ABS]) en un panel de puerta exterior de un automóvil, un panel basculante y un panel trasero fue introducido en un proceso especial desarrollado para la línea de vehículos. Una mezcla formulada de nailon 6,6 y óxido de polifenileno (PPO). Algunos fabricantes de equipos originales europeos también bajaron la temperatura de los hornos de horneado para acomodar PPO para hacer paneles exteriores de la carrocería. La mayoría de las aplicaciones se encuentran en guardabarros de vehículos. La absorción de humedad por el nailon sigue siendo un problema crítico que debe resolverse para satisfacer las necesidades de rendimiento. Algunos de los requisitos especiales para acomodar plásticos a menudo han llevado a los OEM a volver al metal como solución. Además de los termoplásticos, se utilizaron otros dos materiales etiquetados como SMC (compuesto de moldeo de láminas) y moldeado por inyección de reacción (RIM) como paneles de la carrocería. Este tipo de panel de carrocería tiene costos de material más altos que el acero, pero costos de herramientas más bajos y se usa principalmente cuando los volúmenes de construcción son menos de 200,000 vehículos por año. Del mercado total de paneles de carrocería, dichos paneles de carrocería verticales compuestos disfrutaron de una participación del 6%, el aluminio abarcó el 3% y el acero abarcó el 91% hasta 1998. De eso, SMC disfruta de la mayor parte. Un compuesto termoendurecible reforzado con fibra de vidrio, SMC generalmente está disponible en forma de hoja que se enrolla en bobinas intercaladas con una película de plástico para evitar la adhesión. Se fabrica aplicando una mezcla de resina (generalmente un poliéster), rellenos, agente de maduración, catalizador y agente de desmoldeo sobre dos láminas móviles de película de polietileno (PE). La película inferior también contiene fibra de vidrio picado o estera de vidrio. De esta manera, SMC se puede moldear en formas complejas con poco desperdicio. Aparte de la desventaja del volumen de fabricación, la reciclabilidad había sido un talón de Aquiles para los termoestables y, a menudo, les impedía ingresar a este segmento de mercado relativamente grande. Es interesante notar que los sistemas de pintura utilizados en termoplásticos también limitan su verdadera reciclabilidad. Recientemente, para algunas aplicaciones de defensas fuera de línea y en línea, se han intentado soluciones a base de PP-talco y poliolefinas termoplásticas (TPO). Estos se habían probado esencialmente en plataformas de automóviles muy pequeñas. Los plásticos aún no han penetrado los paneles del piso y del techo debido a varias deficiencias de ingeniería. Sin embargo, se están realizando muchos esfuerzos para cambiar esto en autos conceptuales como el Toyota Sienna, que presentaba un sistema de techo corredizo que usa la resina de PC. Por otro lado, los composites plásticos han sido considerados para su aplicación en campanas durante mucho tiempo con solo penetración selectiva en el mercado. Estos incluyen tanto la fibra de vidrio como el compuesto de fibra de carbono con una matriz termoendurecible, pero están lejos de competir en costo con las soluciones metálicas. Las placas de barro son un pequeño panel diseñado a menudo en el IP para permitir la instalación de dispositivos de cabina. Estos están hechos principalmente de SMC para cumplir con los requisitos de rigidez. En resumen, la entrada de plásticos en los paneles exteriores de la carrocería de los vehículos ha sido difícil, pero los plásticos se encuentran en los paneles, guardabarros y capós de ciertos vehículos. Algunos paneles, como los del piso y el techo, aún tienen que utilizar plásticos, pero los autos de concepto están incorporando plásticos en estas áreas. En 1925, los parachoques delantero y trasero se convirtieron en equipo estándar en todos los automóviles. Lo que en ese momento eran simples vigas de metal se convirtieron en componentes de ingeniería complejos que son parte integral de la protección de los vehículos en colisiones a baja velocidad. Los plásticos entraron en estas aplicaciones en la década de 1980 debido a ventajas como su apariencia estéticamente agradable, resistencia a la corrosión, ligereza de peso y facilidad de diseño. La tasa de expansión de los plásticos está delimitada por los metales, pero los diseñadores pueden solucionar esa deficiencia. Los parachoques no tienen que incluirse en la línea de montaje con metales y, por lo tanto, pueden pintarse por separado y luego montarse en el vehículo más tarde. Los parachoques moldeados en color también se han considerado en el pasado, pero eran difíciles de combinar con el color del resto de los paneles exteriores de la carrocería. Versiones reformuladas con alto contenido de relleno de poliolefina termoplástica (TPO), acrilonitrilo-butadieno-estireno (ABS) y mezclas de policarbonato (PC) / ABS se encuentran en aplicaciones de parachoques en todo el mundo. Hoy, TPO domina este mercado en todo el mundo. Aparte de estos polímeros y mezclas, los termoendurecibles a menudo entran en este mercado como productos moldeados por reacción-inyección (RIM). De hecho, RIM fue el primer plástico aprobado para la fascia de parachoques en América del Norte para cumplir con la resistencia a los choques a baja temperatura exigida por algunos fabricantes de equipos originales. Desafortunadamente, debido a la complejidad del proceso, RIM no se pudo fabricar a una velocidad lo suficientemente alta para satisfacer las demandas de las plataformas de automóviles grandes. El tiempo de ciclo más rápido para la producción de piezas está delimitado por la velocidad de la química de curado y la capacidad de la resina para fluir hacia los moldes. Además, la industria automotriz quería alejarse del uso de sistemas de polímeros termoendurecibles que no se pueden volver a fundir. Este atributo de los termoendurecibles fue etiquetado por la industria como no reciclable, y la industria dejó espacio para otros termoplásticos como el TPO que se pueden volver a fundir. Las piezas moldeadas por inyección y reacción están hechas de epoxis de uretano, poliésteres y poliamidas. Un estudio de costo versus desempeño informó que RIM ofrece la mejor característica de costo-desempeño para materiales compuestos y es competitivo con el acero. El futuro de los sistemas frontales de vehículos dependerá de cuán innovadores y amigables con los plásticos estén dispuestos a convertirse los ingenieros OEM . Un ejemplo de un paso tan innovador es el diseño de un sistema híbrido de portador frontal (FEC). El diseño y rendimiento de un sistema híbrido de este tipo, en el que el polifenileno relleno de vidrio largo (LGF PP) diseñado específicamente para la aplicación se unió con metal electrorevestido, en comparación con un FEC tradicional construido de acero y atornillado o soldado al cuerpo. Los paneles Quarter in-white han visto algunas soluciones de plástico, pero han sido una aplicación difícil para materiales basados en PC debido a la necesidad de resistencia al agrietamiento por estrés ambiental asociado con la exposición al combustible. Se han implementado soluciones a base de nailon en algunos coches, pero sufren problemas de estabilidad dimensional causados por la absorción de vapor de combustible. Los plásticos también se han introducido como protectores de los bajos para proteger los metales de la corrosión. Debido a la naturaleza de la aplicación, esta pieza debe tener una fuerte resistencia al agrietamiento por astillas de piedra y abusos similares. Sin embargo, con la nueva tecnología para proteger las piezas metálicas, esta aplicación se ha estancado en algunas áreas geográficas. Aquí en los Estados Unidos, LGF PP y ABS son los dos plásticos predominantes en uso. Los nuevos diseños con capacidades multifuncionales harán que algunas de las soluciones actuales queden obsoletas en el futuro. Sin embargo, los plásticos siempre jugarán un papel importante debajo de la carrocería del automóvil. Las manijas de las puertas exteriores son otra aplicación que ha recurrido a los plásticos para equilibrar la resistencia química y las propiedades mecánicas. Muchos termoplásticos rellenos, como mezclas de PC y tereftalato de polibutileno (PBT), tereftalato de polietileno (PET) y nailon, se han probado o utilizado en esta aplicación, siendo el nailon el claro ganador. Las carcasas de los retrovisores exteriores también utilizan muchas soluciones termoplásticas como ABS, PC / ABS, mezclas de óxido de polifenileno (PPO) y poliestireno (PS), nailon, mezclas de PP y monómero de etileno propileno dieno (EPDM) y ABS resistente a la intemperie. Una vez más, el nailon domina claramente esta aplicación en términos de volumen. Muchas otras partes exteriores continúan adoptando soluciones termoplásticas. Como se explica en este capítulo, los plásticos se han introducido en el exterior de los vehículos, especialmente en aplicaciones de parachoques, pero también como protectores de los bajos y manijas de las puertas exteriores. Sin embargo, las condiciones ambientales y las tensiones han limitado el uso de plásticos en algunas partes exteriores de los vehículos. Se siguen encontrando nuevas aplicaciones automotrices para plásticos, y su futuro dependerá de la innovación de diseñadores y fabricantes de equipos originales.
Historia de las carrocerías de automóviles
Los carros sin caballos originales se inspiraron en el diseño, naturalmente, de sus antepasados inmediatos, los carros tirados por caballos. El chasis proporcionaba fuerza y estabilidad, y la carrocería era una entidad separada. Desde el principio se fabricó fundamentalmente con materiales no ferrosos. Este concepto de chasis más carrocería no fue desafiado seriamente hasta la década de 1920. Si el asunto hubiera permanecido allí durante otros cuarenta años, bien podríamos haber visto una transición suave de la estructura de madera y la lona a las carrocerías de plástico. Los materiales tradicionales para la construcción de autocares se habrían rendido ante los beneficios de diseño, costes y rendimiento cada vez más claros de los plásticos. Por supuesto que no sucedió así. Los inicios de una estructura integral de acero se vieron por primera vez a principios de los años veinte. Durante los siguientes quince años aproximadamente, se hizo un uso generalizado de estructuras monocasco de acero unificado. El enorme crecimiento de la producción de automóviles en la posguerra se basó casi en su totalidad en diseños unificados y, en los últimos años, las nuevas tecnologías han contribuido a que este sistema sea prácticamente inexpugnable para la producción en serie. El lugar de los plásticos El predominio del sistema monocasco se deriva de la consistencia y el costo relativamente bajo de la chapa de acero, la facilidad con la que se puede automatizar la soldadura por puntos y la eficiencia y velocidad de las operaciones del taller de prensado. Otra consideración, que a menudo se pasa por alto, es que la chapa de acero no necesita una reacción química ni un cambio de estado para lograr su forma final. Todos estos son factores fundamentales, que sirven para contradecir algunas de las predicciones demasiado entusiastas escuchadas durante las últimas dos décadas a favor de las carrocerías de plástico para el mercado de volumen. Al ignorar estas realidades, los campeones del plástico pueden hacerle un flaco favor a los plásticos. Frente a las prácticas de los talleres de carrocería de gran volumen, la fabricación, unión y atornillado de paneles de plástico son lentos y costosos. Pero cuando se establecen en los objetivos correctos, no hay duda de que los plásticos pueden tener un éxito extraordinario. El parachoques tradicional ha dado paso ahora a extremos delanteros y traseros integrales completos, en los que los plásticos ocupan un lugar destacado. Esto es característico de todos los coches, ya sean de serie grande o pequeña. Lo mismo se aplica a toda la gama de molduras y piezas "colgantes". Con diferentes ponderaciones, los mismos beneficios de los plásticos se aprovechan en todas estas aplicaciones. El ahorro de peso, la libertad de diseño, la consolidación de componentes y la resistencia a la corrosión son axiomáticos. La investigación y el desarrollo durante muchos años han asegurado otros beneficios: la resistencia a los rayos UV, la capacidad de pintura, la estabilidad dimensional y la resistencia al impacto son ejemplos. Cualquier comparación entre diferentes materiales, en cuanto a su idoneidad para una aplicación, debe estar relacionada con los procesos involucrados y de allí con los niveles óptimos de producción. Para algo tan grande y complejo como la carrocería de un automóvil, el análisis de los puntos de equilibrio es absolutamente crucial. Se deben tener en cuenta factores como la vida útil del modelo, los niveles de producción, los costos de las herramientas, los precios de los materiales y las tasas de producción, así como las fuerzas del mercado menos predecibles. En orden descendente de puntos de equilibrio, los procesos en conflicto (es decir, potencialmente acabado Clase A) siguen esta secuencia:
1. Prensado de acero
2. Moldeo por inyección
3. Moldeado de láminas
4. Moldeo por inyección de reacción
5. Moldeo por transferencia de resina
Varios diseños de vehículos con paneles totalmente de plástico montados en un marco espacial de metal (o con algún otro miembro de refuerzo de acero) tienen estado en producción durante los últimos cuarenta años, con diversos grados de éxito. En la actualidad, el sector más grande comprende lo que se puede describir como híbrido, en el que se incluyen paneles de plástico individuales en una estructura esencialmente de acero. Estos pueden ser desarrollos exploratorios o simplemente ejercicios de reducción de costos. Más interesante (y cada vez más) son parte de una tendencia hacia el empleo de paneles de plástico intercambiables para lograr "estiramientos faciales" y variantes de modelo.
Paneles de carrocería y estructuras Automóviles de plástico
El primer automóvil conocido con carrocería de plástico fue concebido por Henry Ford I como el "automóvil de soja". Se produjo un prototipo en 1941, con un marco de acero tubular que soportaba 14 paneles fenólicos (derivados de hecho del petróleo y no del aceite de soja). Los costos resultaron ser mucho más altos de lo anticipado (¡los paneles se describieron como "¡solo un cuarto de pulgada de grosor"!). El automóvil es mejor recordado ahora por la famosa fotografía de él resistiendo un mazo empuñado vigorosamente por Henry Ford.
En 1945 era un prototipo de estructura de acero tubular similar, fabricado para señalar los méritos de los paneles de plástico reforzados con fibra de vidrio. Los paneles de fibra de vidrio lograron su primer éxito comercial en 1953. Este automóvil fue diseñado con paneles de poliéster reforzado con fibra de vidrio sin soporte en un chasis de escalera de acero. Con muy pocas modificaciones, ha sobrevivido desde entonces, con niveles de producción que generalmente superan los 20000 por año. Los paneles SMC han reemplazado desde hace mucho tiempo al primitivo sistema de colocación manual. La producción total acumulada superó la marca del millón en 1992. Este fue fabricado por el nuevo proceso VARI (Inyección de Resina Asistida al Vacío), en el cual las dos mitades del cuerpo se moldean en herramientas combinadas y posteriormente se unen. El único chasis es una sección de sombrero de copa "backbone" en acero; de lo contrario, la estabilidad del cuerpo está asegurada por vigas integrales de espuma. Estas vigas de espuma se utilizan para ubicar y soportar mechas de vidrio unidireccionales, antes de inyectar la resina de poliéster. El resultado es una carrocería extremadamente fuerte, de la que el actual Esprit es el último ejemplo. El sistema Lotus es extremadamente efectivo, pero no se afirma que alguna vez cubrirá las necesidades de costos y producción del mercado masivo. El proyecto de automóvil deportivo es recordado en Irlanda del Norte como un desastre económico. Sin embargo, como carrocería, era espectacular y único. El cuerpo se fabricó con vigas de espuma de refuerzo, y el estilo se logró revestiendo el cuerpo compuesto con una lámina de acero inoxidable de calibre delgado. Se logró un gran avance en la década de 1960. Utilizaron un proceso que denominaron "Inyección a baja presión", ahora más conocido como Moldeo por transferencia de resina, para producir grandes paneles para vehículos. El progreso en el moldeo por transferencia de resina culminó, en 1986, con el Renault Espace, que ha sido uno de los ejemplos más exitosos de un vehículo con carrocería de plástico con estructura de acero hasta la fecha. Los paneles laterales son RTM, revestidos en molde, con un peso de 28 kg, producidos en un ciclo de 5 minutos. Otros paneles utilizan tanto RTM como SMC rígido; El problema de combinar rigidez y resistencia al impacto en las puertas se ha resuelto mediante el montaje de paneles SMC flexibles en marcos de acero. La rigidez adicional que necesitan los paneles del techo y el capó se obtiene mediante el uso de un núcleo relleno de espuma PUR en un sándwich. Este utilizó cuatro categorías diferentes de material: SMC para los paneles más rígidos (el capó y el techo, un panel relativamente pequeño en este auto deportivo biplaza), RIM y RIM reforzado para los paneles laterales y PP-EPDM moldeado por inyección para los parachoques resistentes a los impactos. El Fiero fue un indicador impresionante del compromiso con los plásticos, y se lograron ventas considerables entre 1984 y 1988. Sin embargo, el diseño, que involucraba un marco espacial de acero bastante pesado, era menos innovador que el proceso de ensamblaje, con sus dispositivos para ubicar el variedad de paneles plasticos. Dos grandes paneles son de SMC, con las alas de poliurea R-RIM. Gran parte de la estructura de la carrocería es de material compuesto, con solo los bajos de acero galvanizado. El APV podría describirse como el enfoque más cercano hasta ahora a un vehículo volumétrico con carrocería totalmente de plástico. En los vehículos con carrocería de plástico considerados hasta ahora, el énfasis se ha puesto por completo en los materiales termoendurecibles reforzados; para los modelos más recientes se han formado mediante procesos "semi-industriales", principalmente SMC, R-RIM y RTM. El primer uso significativo de termoplásticos (descontando algunos intentos valientes pero infructuosos con ABS en la década de 1960). Los diferentes requisitos de los paneles individuales de la carrocería se reflejaron en la elección de los materiales: Paneles horizontales: un complejo sándwich de múltiples capas que involucra tela de vidrio tejida en un sistema epoxi RTM y capas internas de estera de vidrio alrededor de una capa de espuma PUR. Esto asegura una alta rigidez con poco peso, con un rendimiento de fractura mucho mejor que el que se podría lograr con sistemas más simples (¡y más baratos!) Como SMC, además de una excelente absorción acústica. Paneles verticales: molduras de inyección en aleación PC/PBT, termoplástico resiliente. Parachoques: una piel termoplástica, moldeada por inyección en PBT modificado. El diseño en su conjunto pasa las pruebas de impacto de 5 mph en EE. UU., En gran parte debido al vehículo de pasajeros, descrito como un "transportador espacial").
Paneles de debajo de la carrocería
Los paneles de debajo de la carrocería, o escudos de protección, pueden clasificarse como paneles de carrocería no estructurales. Su función es principalmente aerodinámica y, por lo tanto, es más probable que se encuentren en automóviles de alto rendimiento; sin embargo, su función en la protección del compartimento del motor es útil. No se requiere que dichos paneles tengan un acabado de calidad, ni están sujetos a las temperaturas del horno de capa superior. Por tanto, la gama de materiales aceptables es mucho más amplia que la de otros paneles de carrocería. El material más utilizado es el GMT, en forma de esterilla de vidrio impregnada de PP, estampada en caliente. Muchos modelos estadounidenses han utilizado este sistema desde principios de la década de 1980, aprovechando los beneficios de las herramientas de bajo costo y las buenas tasas de producción. Sin embargo, cuando se necesita un conformado y una ubicación más precisos, y cuando los números justifican el mayor costo de las herramientas, algunos fabricantes europeos están recurriendo a paneles moldeados por inyección. Se utiliza un compuesto de moldeado de PP reforzado con fibra de vidrio templado. SMC no se utiliza generalmente para paneles de gran superficie que puedan estar expuestos al impacto de piedras.
_______________________________________________________________________________________________________________________________________________________
Espejos retrovisores
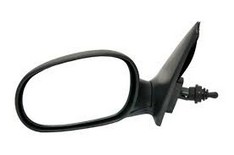
Bases de espejos exteriores
PA6 permite soluciones de peso ligero en comparación con el metal; permite soluciones confiables debido al alto rendimiento de la línea de soldadura y resistencia a la temperatura (mejor que el PP) y a su gran apariencia de superficie (mejor que PA66) y resistencia a los rayos UV. PA6 permite soluciones rentables en comparación con PA66; Los grados dePA6 permiten incluso una mayor rentabilidad debido a la ventaja del tiempo de ciclo del 25% y debido a la alta fluidez que permite diseños de paredes más delgadas
Materiales: XPRENE A 9000
Propiedades: Excelente resistencia UV, excelente resistencia química, resistencia al impacto, excelente apariencia estética, resistencia al rayado, flexibilidad.
_______________________________________________________________________________________________________________________________________________________
Rejillas delanteras galvanizadas
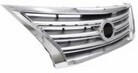
Material : XPRENE 4500
Propriedades: Excelente adhesión de la capa de cromo, resistencia superior al calor, resistencia al impacto, baja deformacion, bajo encogimiento, excelente resistencia química.
_______________________________________________________________________________________________________________________________________________________
Parachoques
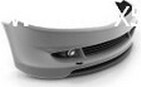
_______________________________________________________________________________________________________________________________________________________
Conjunto de capó de compuesto de carbono (Campanas)
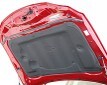
_______________________________________________________________________________________________________________________________________________________
Compuertas
- Un peso más bajo puede reducir las emisiones de CO2
- Una puerta trasera más ligera es más fácil de abrir y cerrar
- Menos peso de la parte superior del cuerpo reduce el centro de gravedad, mejorando el manejo
Las ventanas de plástico de policarbonato pueden reducir el peso aún más.
_______________________________________________________________________________________________________________________________________________________
Podar
_______________________________________________________________________________________________________________________________________________________
Limpiaparabrisas
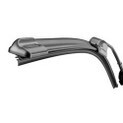
_______________________________________________________________________________________________________________________________________________________
Aletas
_______________________________________________________________________________________________________________________________________________________
Spoilers
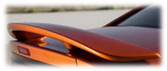
Propiedades: Resistencia al calor, Estabilidad dimensional, Rigidez
_______________________________________________________________________________________________________________________________________________________
Manija de puerta
Material: PA66 30GF (XMID A GF30 UV)